Steel Panelizing Factory
The SFS Steel Panelizing Factory is the largest and most effective system Jobsite has engineered. The automated system includes a complete software package that gives you full control of building design as well as control of inventory and production management.
The roll forming production and assembly lines work in one cohesive unit for maximum efficiency during production. This system is tested and proven and is, by far, the most cost effective solution for quickly and effectively producing steel frame panelizing for residential and commercial applications.
Typical Equipment Layout of a
Steel Panelizing Factory
The complete factory requires minimum of 30,000 SF of warehouse space.
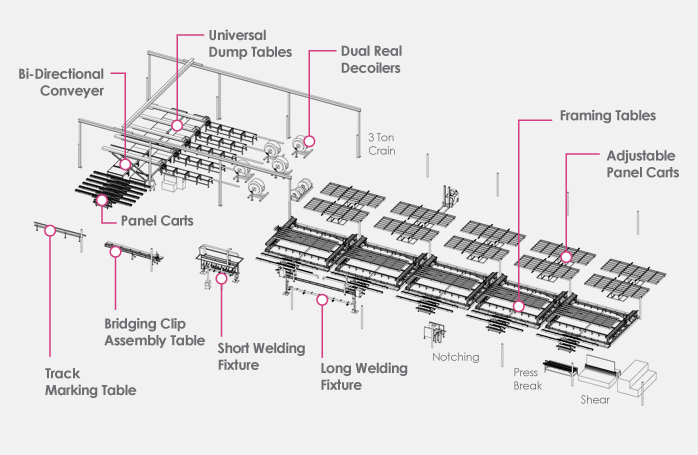
Benefits of a SFS Steel Panelizing Factory
1. Accelerate Speed of Construction.
With 80% of the framing assembled off-site, builders can expect to cut the speed of framing by an amazing 70%.
2. Lower Building Costs
Lower all costs of construction including labor, waste, long term building maintenance, foundation costs, scrap disposal costs and weather delay costs.
3. Customizable
Each system is setup to fit your business model. After consulting with Jobsite’s engineering department and steel framing experts a system is developed to meet your needs.
Detailed Product Component Information
Bi-Directional Conveyor
The Jobsite Bi-Directional Conveyor is capable of delivering parts to either end of the conveyor allowing you to feed two (2) separate lines. Single conveyors handle parts up to 10’ in length and dual conveyors will handle parts up to 24’ in length.
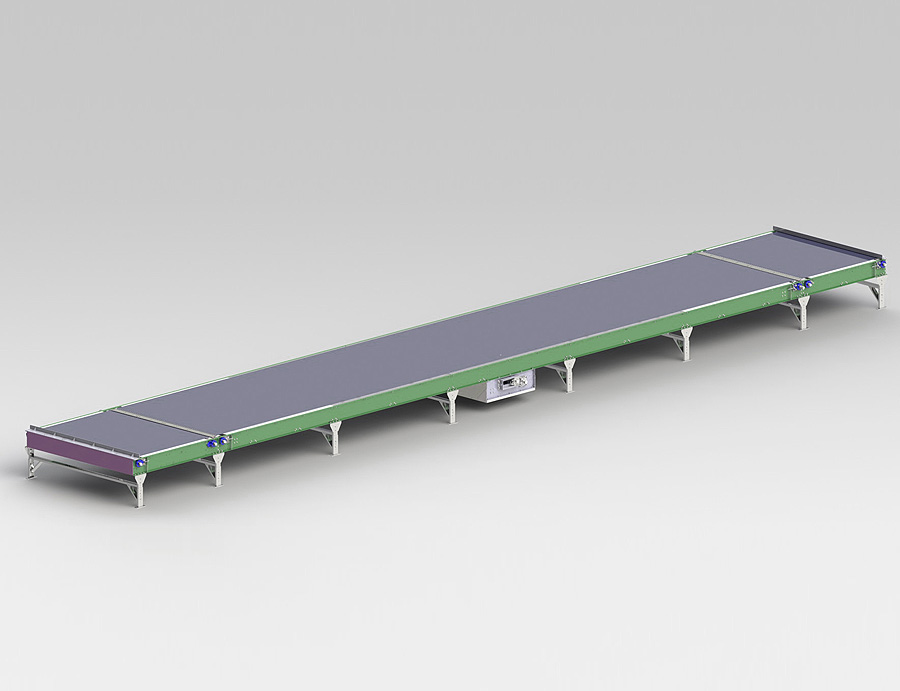
Universal Dump Table
The Universal Dump Table is attached to each machine to handle the parts being made. Operated by a pneumatic cylinder, parts can be dumped onto the conveyor operating in either direction. The dump zone clear sensors handles part lengths from 6” to 24’.

Bridging Clip Assembly Table
The Bridging Clip Assembly Table is designed for attaching clips to the inside or outside of steel studs. Handles stud sizes from 3 5/8” to 10”.
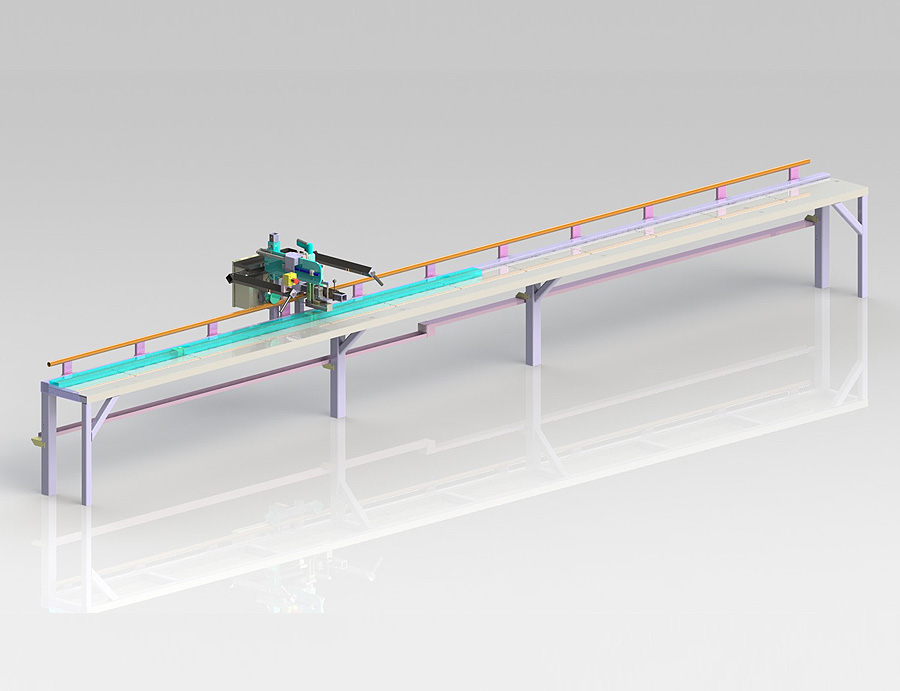
Material Transfer Cart
The Material Transfer Cart is used for transporting parts from the conveyors through the factory.
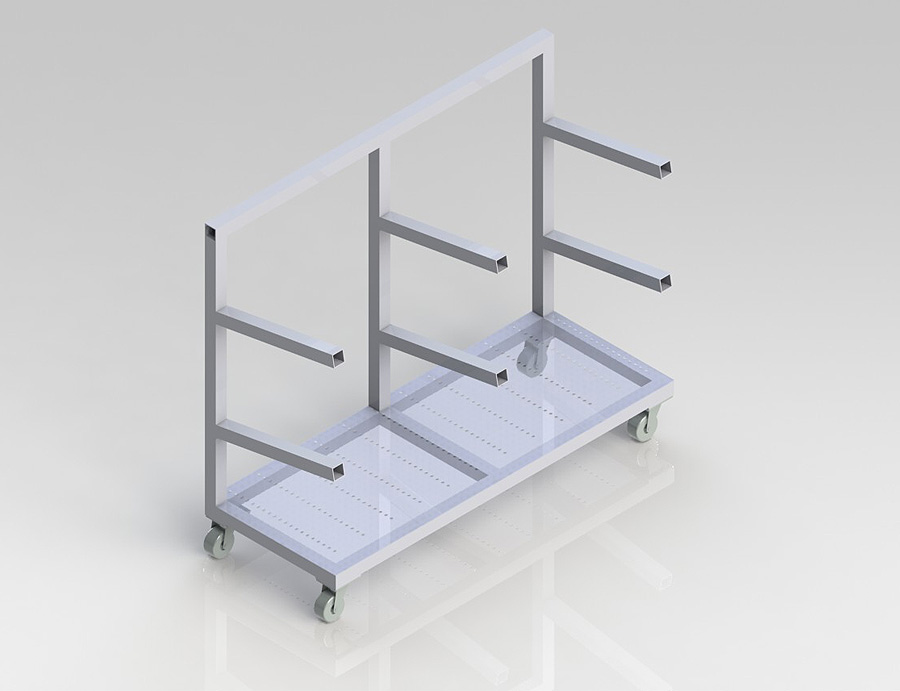
Short Welding Fixture
The Short Welding Fixture is designed for welding steel studs together to create support beams and columns. It handles stud sizes from 3 5/8” to 10” up to 12’ long.
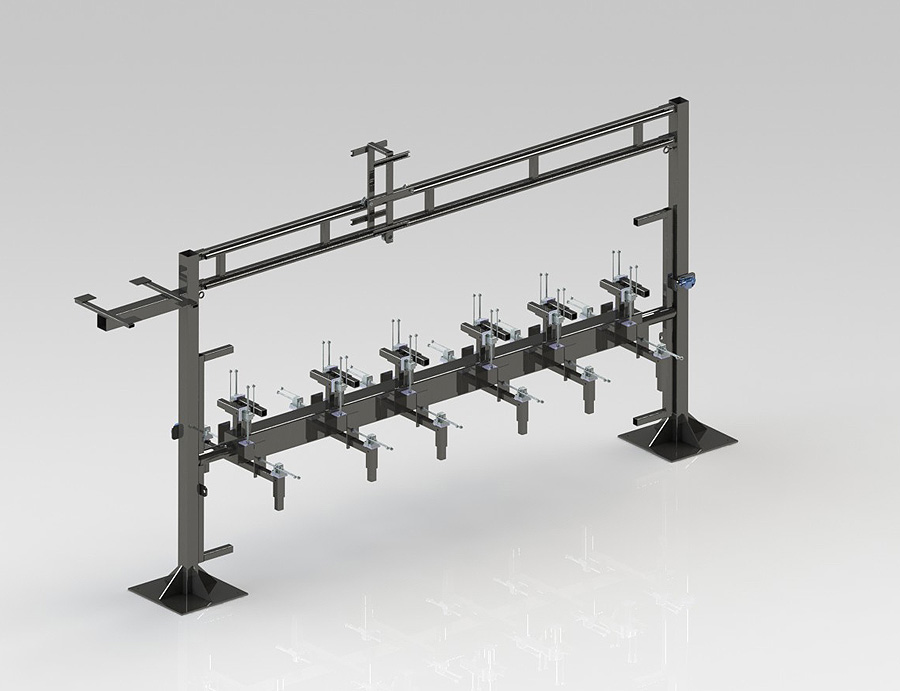
Long Welding Fixture
The Long Welding Fixture is designed for welding steel studs together to create support beams and columns. It handles stud sizes from 3 5/8” to 10” up to 26’ long.
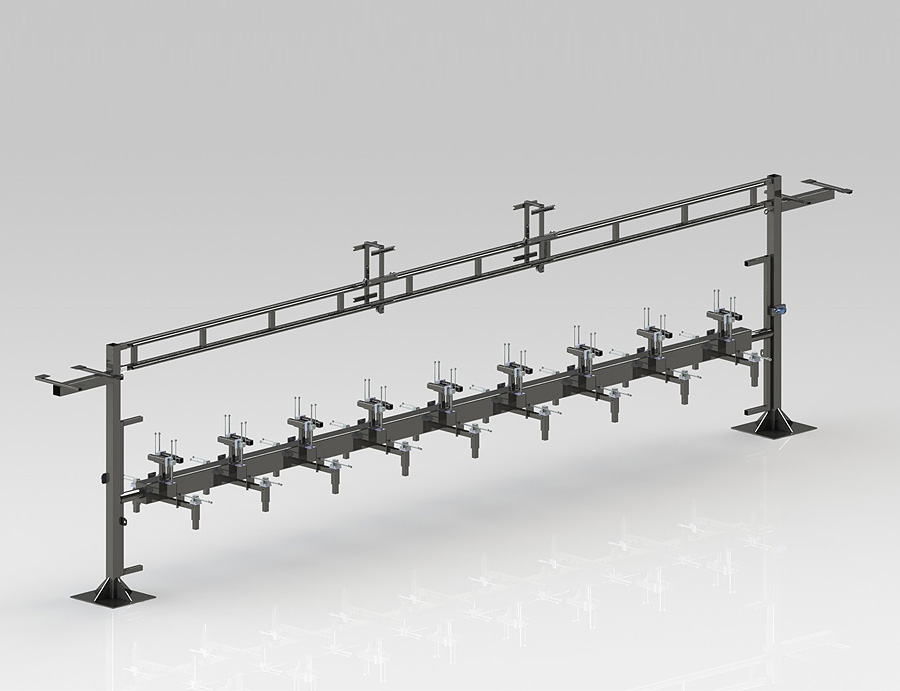
Adjustable Height Panel Cart
This Cart is designed for moving wall panels to various sub-assembly locations. It handles panel sizes from 4’ to 26’ high to 22’ wide. Powered by battery they have 24” of vertical movement. A welding cart is available to easily allow for panel welding.
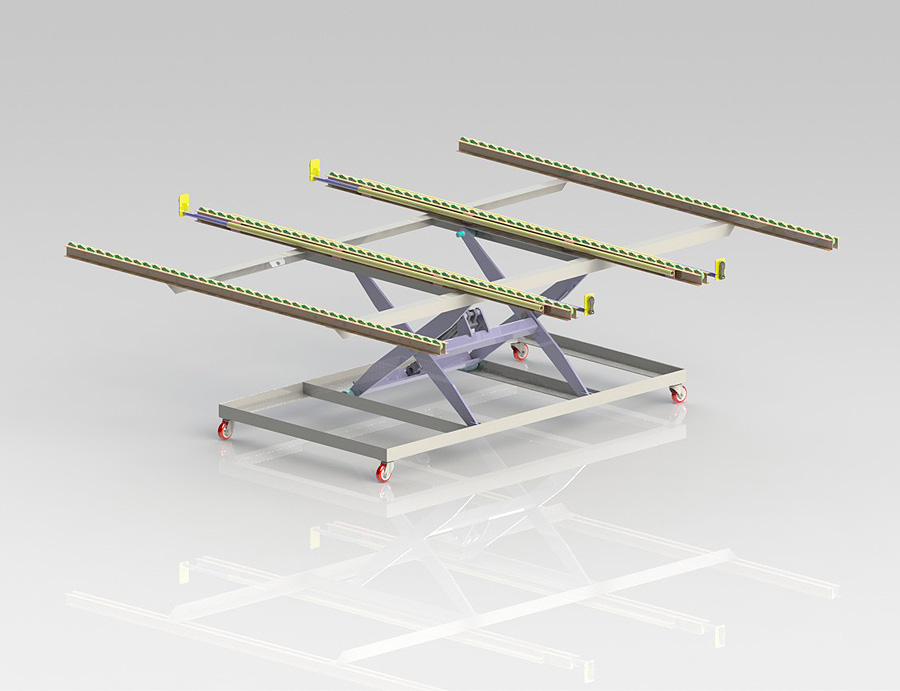
Framing Table
The Framing Table is designed to easily assemble steel stud and track members into wall panels. It handles wall panel sizes from 4’ to 26’ high and 22’ wide.
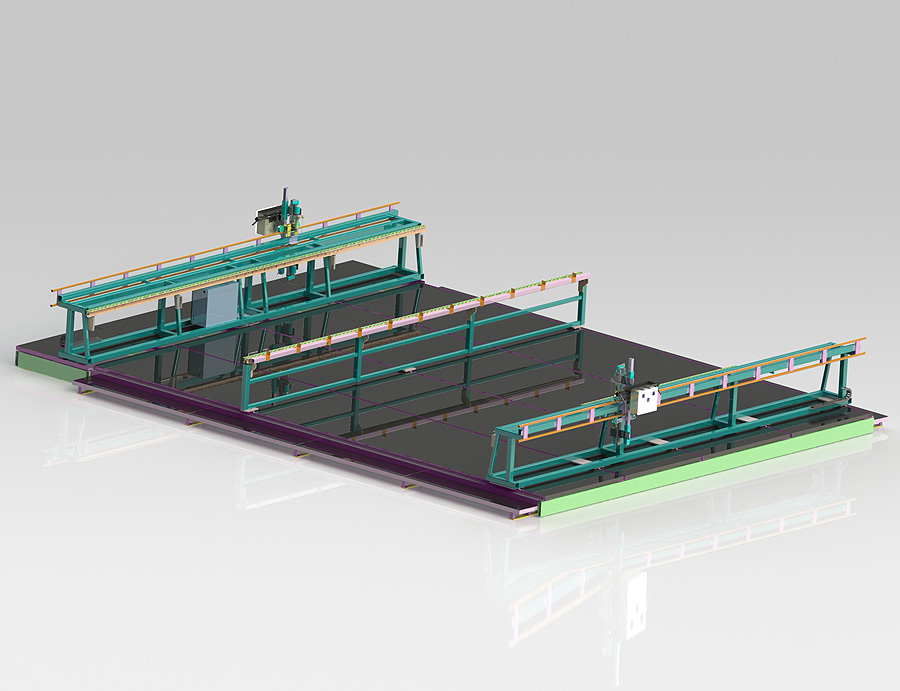
L-Skid
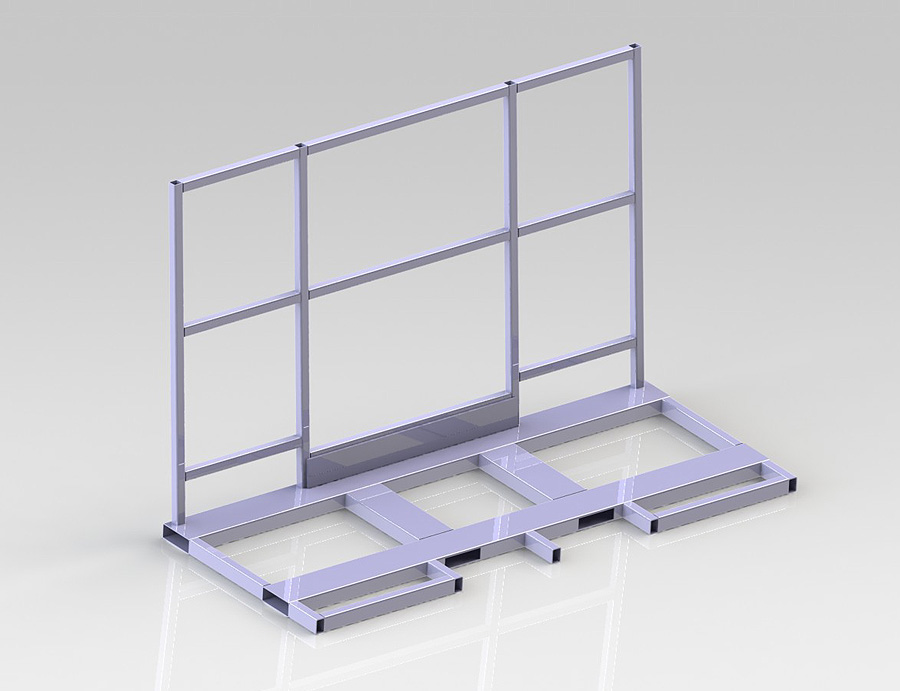
Truss Tables
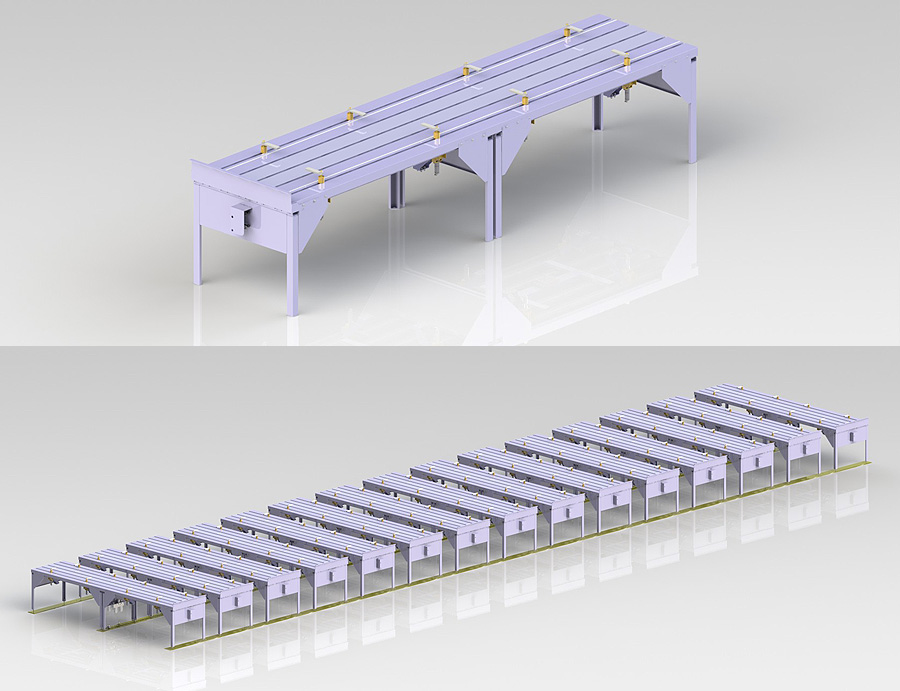
Features
- Bosch Rexroth controls and drive for accuracy and history of excellent reliability
- Servo driven punch provides close tolerance accuracy and none stop punching for increased production, with interchangeable tooling for different hole sizes and shapes. Maximum size is 1 1/2″ (38.1mm) X 3 1/2″ (88.9mm) obround
- Includes 3 Stud and Track kits: 3 5/8″ (92.07mm), 6″ (152.4mm), 8″ (203.2mm) sizes – 1 5/8″ and 2 1/2″ options are available
- Hydraulic shear with quick change dies
- Nitride Hardened rollers designed for long life for running galvanized steel
- Material oiler / mister to aid in keeping the rollers clean when running galvanized material
- Safety interlocks on all sliding covers that meet OSHA requirements
- Emergency stop buttons on both ends of the machine
- Safety stack lights on machine and decoiler indicates equipment in operation
- 24 month limited warranty on Jobsite manufactured parts, excluding wearable parts, (shear/punch parts) and manufactures warranty on purchased parts
Specifications
- Length: 245″ (6.22 m)
- Length with options: 305” (7.75m)
- Width: 44″ (1.12 m)
- Height: 65″ (1.65 m)
- Weight: 5,900 Pounds (2,676 kg)
- Equipment Power Requirement: 380/460V, 3ph/50/60Hz, 30 Amp
- Main Servo Drive: 203.5 in lbs/ 23.0 NM continuous torque (x3 peak)
- Punch Servo Drive: 70.8 in lbs/8.0 NM continuous torque (x3 peak)
Options
- 2 1/2″ (63.5mm) stud and track kit for 26 to 14 gauge steel
- 1 5/8″ (41.3mm) stud and track kit for 26 to 20 gauge steel
- Heavy Duty Dimpling / Pre-Punching for precision screw positioning in 26-14 gauge material (3 1/2″, 6″ and 8″ stud and track only)
- Internet connectable diagnostics available to aid in trouble shooting
- Vertex BD Framing Software
- Stand-Alone Crane System
- Semi-Auto Manual Unload Table for stud and track roll formers
- Any material size Imperial or Metric
- Customize stud & track kits sizes from 3 5/8” to 8” or metric sizes
- 6,000lb Single Reel De-coiler 17”- 24” (0.430m – 0.610m)
- Dual Reel De-coiler
- Ink Marking System
- Containerized machine